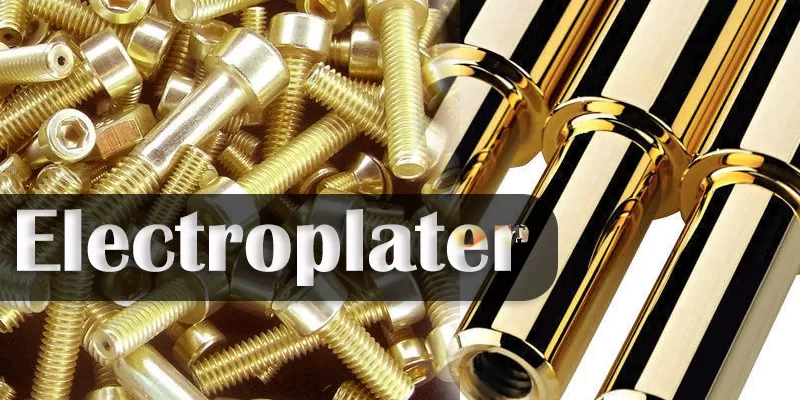
🔹 Electroplater Trade – Course Overview
Duration: 2 Years | Approved by NCVT
The Electroplater trade is designed to equip candidates with specialized skills in metal finishing, coating, and electrochemical deposition techniques. Over two years, candidates receive training in Professional Skills, Theoretical Knowledge, Engineering Drawing, Workshop Calculation & Science, and Employability Skills. In addition to structured coursework, candidates undertake project work and extracurricular activities to enhance their confidence and industry readiness.
🔹 Key Learning Components
1️⃣ Professional Skills & Practical Training
Candidates gain hands-on experience in:
✔️ Surface preparation techniques (cleaning, polishing, degreasing, pickling)
✔️ Electroplating process for various metals (nickel, copper, zinc, silver, gold, etc.)
✔️ Chemical preparation and handling of plating solutions
✔️ Electrochemical principles and electrolysis process
✔️ Operating plating tanks and rectifiers
✔️ Troubleshooting plating defects and implementing corrective measures
✔️ Metal finishing techniques like anodizing, passivation, and chromating
✔️ Testing and quality control of plated surfaces
✔️ Environmental and safety regulations in electroplating
2️⃣ Professional Knowledge
✔️ Basic Electricity & Electrochemistry – Understanding current, voltage, resistance, and their effects in plating
✔️ Properties of Metals & Alloys – Conductivity, corrosion resistance, and adhesion properties
✔️ Electroplating Techniques – Barrel plating, rack plating, brush plating
✔️ Types of Electroplating Solutions – Acidic, alkaline, cyanide, and non-cyanide solutions
✔️ Plating Equipment & Machinery – Rectifiers, anode and cathode setup, agitation methods
✔️ Chemical Reactions & Solution Maintenance – Controlling pH, temperature, and composition
✔️ Quality Testing & Defect Analysis – Thickness measurement, adhesion test, and visual inspection
3️⃣ Engineering Drawing
✔️ Reading technical drawings & blueprints related to plating work
✔️ Understanding geometrical symbols and tolerances
✔️ Sketching plating layouts & workpiece designs
4️⃣ Workshop Calculation & Science
✔️ Basic mathematics & measurements used in plating thickness and bath concentrations
✔️ Chemical calculations for solution preparation
✔️ Physics & chemistry applications in electroplating processes
5️⃣ Employability Skills
✔️ Workplace safety & environmental awareness
✔️ Communication skills – Verbal & written for documentation
✔️ Entrepreneurial skills for self-employment in the electroplating industry
✔️ Computer basics for record-keeping and process automation
🔹 Additional Training & Activities
✔️ Project Work – Industrial plating assignments, innovative coating methods
✔️ Industry Visits – Exposure to real-world electroplating units
✔️ Extracurricular Activities – Workshops, exhibitions, and skill competitions
🔹 Career Opportunities
After completing the Electroplater Trade, candidates can work in:
✅ Manufacturing & Automobile Industries (chrome plating, corrosion protection)
✅ Jewelry & Decorative Coating (gold/silver electroplating)
✅ Electronics & Electrical Industry (PCB plating, connector finishing)
✅ Aerospace & Defense Sectors (precision coating of aircraft parts)
✅ Metal Finishing & Surface Treatment Plants
✅ Self-Employment – Start your own electroplating business
🚀 Why Choose Electroplater Trade?
✔️ Industry-relevant skills for high-demand jobs
✔️ Hands-on training with modern plating techniques
✔️ Opportunities in both domestic & international markets
✔️ Pathway to self-employment & entrepreneurship
FIRST YEAR: In this year, the trainee learns about safety and environment, use of fire extinguishers and various safety measures involved in the industry. He gets the idea of trade tools &machineries, practices on filing, hacksawing, planning, drilling, marking, cutting and chipping etc. Identifies different types of conductors, cables, prepare wire joints and learns crimping and soldering. Knowledge of basic electrical laws like Kirchhoff’s law, ohm’s law, laws of resistances and their applications. The trainee learns installation, testing and maintenance of batteries and wiring of panels. The trainee gets the idea of basic process of electroplating.
The trainee learns to handle different solutions, treatment of hazardous chemicals, safety precautions in electroplating shop, first aid and antidotes for chemical poisoning. Preparation of articles before plating, different types of cleaning like polishing, buffing, blasting, electro-cleaning, ultrasonic cleaning and vapour degreasing etc. Skilling practice on Nickel and Bright & Hard Chromium plating by different methods, various defects generally encountered in plating, causes for these defects, their remedies and various methods to remove defective deposits.
SECOND YEAR: The trainee learns setting up of various electroplating baths. Prepares solutions and practices on Zinc, Cadmium, Tin, Brass, Silver and Gold plating on ferrous/ non-ferrous metals by different methods and passivation with various colours. He understands various defects generally encountered in electroplating, causes for these defects and their remedies. Skilling practice to remove defective deposits on different metals by immersion and electrolytic methods. The trainee practices on electroplating of small articles by Barrel plating method for the plating of Copper, Nickel, Tin, Zinc and Cadmium.
In this year, the trainee learns about electroless method of plating for Copper, Nickel, Tin, Silver and Gold. General defects, their causes and remedies in electroless plating. Electroplating on Aluminium with zincate dipping process. The trainee practices on plating of Copper, Nickel, Chromium, Silver and Gold plating on non-conductive surfaces like ABS plastic. He prepares PCBs with Copper, Nickel, Tin, Silver & Gold and practices chemical etching for Copper & Brass. Skilling practice on Anodizing, methods of various colouring techniques, conversion coating, chemical milling on aluminium, phosphating, power coating, metalizing and passivation process. Conducts various tests viz., adhesion, porosity, thickness, corrosion resistance etc. and carries out preventive and breakdown maintenance of electroplating shop machineries.
TRAINING SYSTEM
The Directorate General of Training (DGT) under Ministry of Skill Development & Entrepreneurship offers a range of vocational training courses catering to the need of different sectors of economy/ Labour market. The vocational training programmes are delivered under the aegis of Directorate General of Training (DGT). Craftsman Training Scheme (CTS) with variants and Apprenticeship Training Scheme (ATS) are two pioneer schemes of DGT for strengthening vocational training.
Electroplater trade under Craftsman Training Scheme is delivered nationwide through network of ITIs. The course is of two-year duration. It mainly consists of Domain area and Core area. The Domain area (Trade Theory & Practical) imparts professional skills and knowledge, while Core area (Workshop Calculation & science, Engineering Drawing and Employability Skills) imparts requisite core skill, knowledge and life skills. After passing out the training program, the trainee is awarded National Trade Certificate (NTC) by DGT which is recognized worldwide.
Trades Summery:
Brief description of Job roles:
- Carryout Installation, maintenance & repair works of Electrical AC/ DC machinery, lighting circuits and equipments used in industries.
- 5S & Housekeeping awareness and techniques.
- Use, handling and storage of hazardous chemicals.
- Troubleshooting of electrical items used in plating.
- Practice on using fitting, carpentry and sheet metal tools.
- Use of electrical instrument (analog/digital) like voltmeter, Ammeter, Wattmeter, Energy Meter, Wheatstone bridge, oscilloscope, Earth tester, Tong tester, Megger etc to measure to different electrical quantities.
- Carry out Wiring & Earthing System.
- Carry out surface finishing process prior to plating.
- Carry out electroplating process on various metals and metal alloys.
- Carry out electroplating on plastics and other non-metallic surfaces.
- Carry out electroplating on precious metals.
- Carry out electroless nickel and electroless chrome plating.
- Carry out plating according to specific user benefits.
- Carry out Hot dipping process & electroplating (granadising).
- Carry out anaodizing and Galvanizing processes and metal colouring
- Carry out plating on PCB’s; heat treatment, conversion coating, masking and stripping process
- Carry out the work to minimize contamination and effluent treatment and other safety control measures
- Quality test for plated work and correction of faults.
Electroplater; gives coating of gold, silver, nickel, chromium, copper etc. of required thickness to metal parts by electrolytic process. Examines strength of metallic solution and sets anode plates (positive terminal) in solution. Suspends de-greased components well dipped in side plating solution and connects cathode (negative) to it. Regulates current and allows components to remain dipped in solution for specific period depending upon type and thickness of plating required. Removes components and swills them in hot and cold water baths. Dries them in sawdust or centrifugal air dryer. Transfers components to unrigging rack or other specified place for policing. May prepare plating solution under guidance of shop supervisor. Is designated as Gillder if engaged in gold platting and Anodiser if colours aluminium and light alloys article using specific chemical solutions.
Surface Treatment Technician; is responsible for conducting electroplating, powder coating and Anodizing operations as per the product and the customer requirement to ensure that the surface of the metallic body becomes resistant to chemicals, moisture and other wear and tear.
Galvanizer; applies coating of zinc on ferrous articles by dipping them in molten zinc. Checks and controls quantity, quality and temperature of acid (hydrochloric acid), flux (zinc chloride) and zinc baths. Preheat articles if necessary and dips or passes them either manually or mechanically through, acid, water, flux and zinc baths successively at controlled speed. Skims dirt from baths and continues operation with necessary adjustment of solution, temperature etc., ensuring regular and uniform coating. May similarly apply tin coating using palm oil as flux and be designated as Tin Plater or Tinning Machine Operator. May regulate temperature by gauges and by colour of melting metals.
LEARNING OUTCOME
Learning outcomes are a reflection of total competencies of a trainee and assessment will be carried out as per the assessment criteria.
FIRST YEAR:
- 1. Prepare profile with an appropriate accuracy as per drawing following safety precautions.
- 2. Prepare electrical wire joints, carry out soldering and crimping.
- 3. Verify characteristics of electrical and magnetic circuits.
- 4. Carry out Installation, testing and maintenance of batteries with due care and safety.
- 5. Perform wiring, installation of electrical accessories and earthing of electrical equipment.
- 6. Construct small electronic circuits as per drawing using basic electronic components.
- 7. Explain principles and basic process of plating one metal onto another by electrolysis. Use laboratory apparatus and estimate pH, mass, normality, conductivity, specific gravity etc.
- 8. Handle different solutions with due care & safety and undertake metal treatment processes and effluent treatment of hazardous chemicals in electroplating workshop. Prepare chemical solutions and undertake cooling, heating, filtering, agitating and other treatments for solutions. Carry out analysis of chemical baths with Hull cell process.
- 9. Plan and perform all the various aspects of the plating process including surface preparation, mechanical cleaning like polishing, buffing, blasting etc. and chemical cleaning like electro cleaning, ultrasonic cleaning, vapour degreasing, pickling, rinsing, masking etc.
- 10. Plan and perform Copper plating using different methods, examine various defects in Copper plating, causes and their remedies. Remove defective copper deposit by different methods.
- 11. Plan and perform Nickel plating using different methods, examine various defects in Nickel plating, causes and their remedies. Remove defective nickel deposit by different methods.
- 12. Plan and perform Bright and Hard Chromium plating by different methods on ferrous and non-ferrous metals, examine various defects in Chromium plating, causes and their remedies. Remove defective chromium deposit by different methods.
SECOND YEAR:
- 13. Plan and perform Zinc plating by different methods, examine various defects in Zinc plating, causes and their remedies. Remove defective zinc by different methods.
- 14. Plan and perform Cadmium plating by different methods, examine various defects in Cadmium plating, causes and their remedies. Remove defective cadmium deposit by different methods.
- 15. Plan and perform Tin Plating by different methods, examine various defects in Tin plating, causes and their remedies. Remove defective tin deposit by different methods.
- 16. Plan and perform Silver plating by different methods, examine various defects in Silver plating, causes and their remedies. Remove defective silver deposit by different methods.
- 17. Plan and perform Gold plating by different methods, examine various defects in Gold plating, causes and their remedies. Remove defective gold deposit by different methods.
- 18. Plan and perform Brass plating, examine various defects in Brass plating, causes and their remedies. Remove defective brass deposit by different methods.
- 19. Perform Barrel plating method of electroplating for the plating of copper, nickel, tin, zinc and cadmium.
- 20. Plan and perform electroless plating of copper, nickel, tin, silver and gold.
- 21. Plan and perform plating of copper, tin, nickel, zinc, cadmium etc. on aluminium with Zincate dipping process.
- 22. Plan and perform plating of copper, nickel, chromium, silver and gold on non conductive surface like plastic.
- 23. Make Printed circuit board with copper, nickel, tin, silver and gold. Perform chemical etching processes for copper and brass.
- 24. Plan and perform Anodizing to convert metal surface into a decorative, durable and corrosion resistant by different methods. Examine various defects generally encountered in anodising, causes and their remedies. Remove the defective anodised film by various methods.
- 25. Plan and perform various colouring techniques on anodised aluminium by different colouring dyes and other methods like electro colouring.
- 26. Perform various conversions coating process on aluminium, magnesium and its alloys. Perform chemical milling on Aluminium and undertake passivation of stainless steel.
- 27. Plan and perform phosphating, powder coating and metallizing on various metals.
- 28. Perform quality control aspect of the job and ensure electroplated surfaces are free of any flaws or defects. Perform various tests viz., adhesion, porosity, thickness, corrosion resistance, anodic coating on aluminium, chemical analysis of electrolytes and identification of deposits etc.
- 29. Prepare layout of electroplating plant, estimate cost, materials and accessories required for electroplating shop. Carryout preventive and breakdown maintenance of machines in electroplating shop.